Chemical Industry
Industrial chemistry / Chemical industry
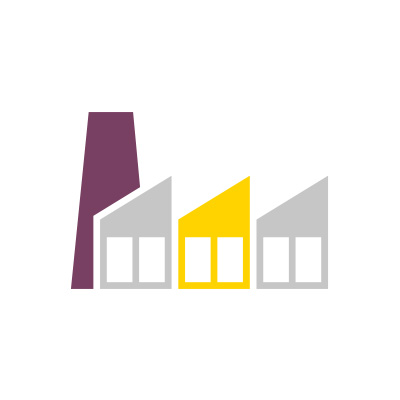
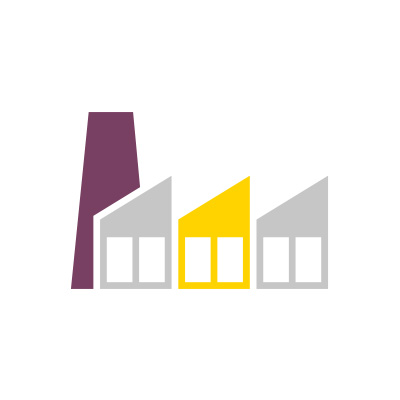
As one of the most successful branches of industry, the chemical industry is under enormous pressure to innovate – one of the reasons for this being society’s ongoing globalisation. Research and development in the various sectors of chemistry therefore plays a key role.
Chemistry provides solutions for many everyday problems. When something goes wrong, we go out and buy glue to repair the damage. When someone falls ill, an antidote is available for treatment in many cases. And if not, this can be developed. Diseases that were long regarded as incurable are nowadays treated successfully. The chemical industry can meet the many specific requirements regarding materials and find solutions for diverse problems.
Organic and inorganic raw materials
Chemical products are indispensable for major branches of industry, for instance the pharmaceutical and automotive sector, as well as the plastics, food, agricultural or building materials industry. Both organic and inorganic raw materials are required here.
Many inorganic raw materials that are required in larger amounts and which cannot be found in nature are produced inexpensively using mass production plants in industrial chemistry. These include basic chemicals such as iron, from which steel is produced for the manufacture of machines and tools, or sodium carbonate (soda) as a cleaning agent.
The chemical production of iron from its ores goes back far into the past. The discovery of iron – and the tools or weapons that can be made from it – is so significant that historians have named this era the Iron Age. The importance of iron grew tremendously during the industrial revolution. In modern blast furnaces iron ore is reduced to iron in a multistage process involving the addition of atmospheric oxygen.
Another important process is the Solvay process – named after a Belgian chemist – for the production of sodium carbonate. Sodium carbonate and calcium chloride are derived from calcium carbonate and sodium chloride. As the reaction does not occur spontaneously, ammonia – as a sort of catalyst – is added in this cyclic process.
In the chlor-alkali process, sodium chloride is split into chlorine gas, sodium hydroxide and hydrogen by means of electrolysis. As these products are always produced in the same ratio, they are referred to as co-products.
The Haber-Bosch process was the first method to produce large amounts of ammonia. In this process, the nitrogen from the air is made to react with hydrogen at 500°C and 300 bar. According to Le Chatelier’s principle, the formation of ammonia is facilitated at high pressure (4 gas particles become 2 gas particles). An iron catalyst is necessary for the reaction to succeed.
N2 + 3 H2 → 2 NH3
The hydrogen required for this is produced in a synthesis gas reactor. Here methane – the main component of natural gas – is made to react with water to produce carbon monoxide and hydrogen.
CH4 + H2O → CO + 3 H2
The carbon monoxide is oxidised with atmospheric oxygen to form CO2 and then scoured to yield pure hydrogen. This can be used for ammonia synthesis.
The ammonia produced in this way is primarily used in the Ostwald process. Here ammonia is oxidised in several stages to form nitric acid.
NH3 + 2 O2 → HNO3 + H2O
Approx. 60% nitric acid results. This can be further processed into nitrates and fertilisers.
Petrochemicals
Many organic raw materials are based on petrochemicals. Petroleum and natural gas – consisting of aliphatic and aromatic hydrocarbons – are split into fractions and processed further into a wide variety of derivative products. These typically serve as educts for drugs, plastics, surfactants, dyes and fuels. Direct products of steam cracking are gases such as ethane and ethene – while isoprene, ammonia, acetic acid and methanol are also attained. Some of these products are important monomers for the plastics industry, e.g. for the production of polyethylene or vinyl acetate. The latter can polymerise easily and serves as a raw material for paper and textile manufacturing. Adipic acid and caprolactam are starting materials for the production of nylon and Perlon.
Flavour & fragrance – scents from petrochemicals
Petrochemistry paves the way for scents. As large amounts of substance are required for the field of flavours and fragrance, natural sources are inadequate. Industry consequently makes use of fragrances derived synthetically. These are produced for perfumes, scented candles, oils, detergents and cleaning agents. The naturally occurring compound limonene was able to be manufactured for the first time by heating isoprene. It can also be attained by extraction from orange juice. Examples of other fragrances and flavours from our portfolio include citronellol, geraniol, linalool and coumarin. The scent of jasmine can be attained by the synthetic product Jasmonal. Not only an orange blossom scent but also a strawberry taste are derived form ethyl-2-naphthyl ether.
Oils are also used as coolants for dispersing resultant heat. Good electrically insulating properties are often expected from a coolant. Special organic ethers are used for this purpose. In contrast to their predecessors, they are non-flammable and also biologically degradable, which means they are not harmful to the environment.
Diverse fields of application: Aeronautical engineering, building materials industry, cosmetics and office routine
The chemical industry also serves aeronautical engineering. Besides materials such as silicones and plastics such as polyetherimides, fine and special chemicals are needed for coatings and paints. We contribute towards technological advancement in aviation, for instance with electrode materials for the development of new batteries.
Lubricants are produced for the building materials industry. They are intended to prevent contact corrosion or adhesions. That makes a lubricant versatile in use. Solid lubricants include graphite, molybdenum disulphide as well as Flonium or Teflon. Cooling lubricants are intended to prevent friction in production plants, while enabling resultant heat to dissipate. Cooling lubricants and lubricating greases also provide protection against corrosion through their additives. Graphite, ceramic particles and plastics are used for manufacturing processes subject to high heat loads.
A distinction is made between natural and synthetic components in the cosmetics industry. They are used in substance mixtures for body care, dental hygiene and skin protection. Other applications include preservatives for extending the shelf life as well as antibacterial agents. Ingredients such as sodium lactate serve to protect the skin from becoming dry. Phthalic acid esters, panthenol, zinc oxide and tocopherol can often be found in cosmetics, shampoos and conditioners too. Above all, lactic acid helps improve skin complexion.
Likewise, disinfectants would not be possible without the chemical industry. Oxidants that split off oxygen have a bactericidal effect. In many cases, this property has a positive role in the fight against many viruses. Alcohols such as ethanol and isopropanol are used for disinfecting surfaces and instruments. In addition, peracetic acids, hydrogen peroxide and chloramine T are used in medicine and technology owing to their high bactericidal effect as a disinfectant. Thanks to their antiseptic effect, products such as chloroxylenol, triclosan, chlorhexidine and povidone-iodine are used for disinfection of the skin and mucous membrane.
Everyday office life would be unthinkable without chemistry. Whoever wishes to print needs ink! The fine powder of a toner comprises synthetic resin, magnetisable metal oxides, pigments, thinners and other additives, and is similar to a liquid. In transfer liquids, pigments with a particle size of less than 1 μm are dispersed in the colourant, which enhances the print quality considerably. Printers worked with toxic heavy metals in the early days – fortunately this has long been replaced by silicon and other more environmentally friend alternatives.
Basic elements for 3D printing
In the automobile industry/automotive and medical/pharmaceutical sectors, production sometimes involves 3D printing. Additive manufacturing allows the desired product to be built up in layers through material deposition. Materials for this can typically be plastics or also metals. This lets prototypes become available sooner, thereby speeding up product development. For plastics with mostly thermoplastic characteristics, we offer basic elements such as 4.4’-difluorobenzophenone, bisphenol A, acrylonitrile and styrene.
It is clear that the automotive sector is undergoing a radical transformation. The focus here is on battery-powered electric vehicles. Stricter emission regulations along with a shift towards more lightweight design entail significant changes in the raw materials needed. These mostly involve aluminium compounds. They reduce weight and are suitable for 3D printing.
Other products required in large amounts for the automotive industry include activated carbon for air filter systems and acrylate-based plastics (windows, foot mats).
A large number of products manufactured on an industrial scale can also be found in the abcr catalogue in practical small quantities for use in the laboratory. For applications in production, we provide many products in bulk. In most cases, packaging in diverse containers according to customer requirements is possible.