Rubber & Plastics
Monomers and polymers at abcr – not only silanes
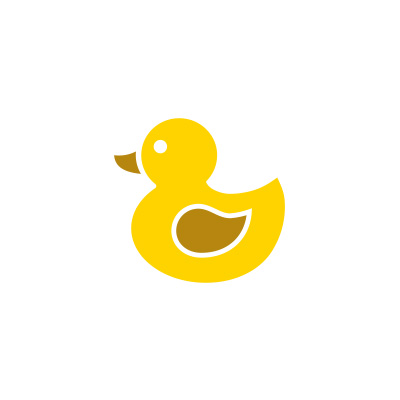
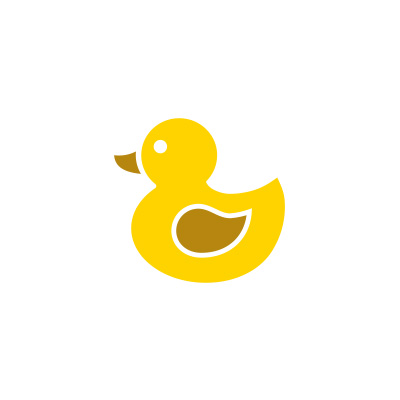
Plastic, synthetics, rubber – these are common terms for materials chemically referred to as polymers, which consist of small building blocks (monomers).
The term “monomer” refers to low molecular organic compounds with reactive functional groups that are converted under catalytic conditions into long-chain polymers. A differentiation is made between homopolymers, which consist of a monomer and copolymers, which are produced from at least two different monomers.
Large-scale technological examples
Especially polyethylene (PE) and polypropylene (PP) have been used as foils for packaging.
The automotive industry uses a range of polymers. One of the most noted is probably polymethylmethacrylate (PMMA), which is used as safety glass for windshields. Tyres, instrument panels, seats, carpets and parts of vehicle bodies are also made from polymer materials.
Coatings of Teflon (PTFE, polytetrafluorethylene) have an anti-adhesive effect and are, for example, used for frying pans.
Siloxanes or silicones with the general structure R3Si−[O−SiR2]n−O−SiR3 (R = hydrogen, alkyl or other organic rest) are not only included in the abcr pallet under commercially available polydimethylsiloxanes (PDMS), which are offered as oils with various viscosities. We also synthetise customised and highly pure products for medical applications or specifically functionalised siloxanes.
Although silicon oils contain the element silicon just like silanes, they are not comparable in regard to their properties, but even opposite in part. Thus, silicone oils are used in foundries e.g. as mould release agents or flow aids.
Functionalised siloxanes are often optimised for an application; i.e. organic groups are introduced into the molecule chains, which subsequently create a special surface characteristic or are suitable for crosslinking just like methacrylic units. Water and oxygen-permeable contact lenses are the best-known example as these consist of so-called macromers.
Here you can learn more about
- Additives
- Polystyrenes
- Acrylates and polyacrylates
- Further monomer and polymer classes at abcr
- Catalysts for polymerisation and oligomerisation
Additives
Additives, e.g. filling and reinforcing substances, can improve the properties of rubber articles or plastics. Their usage can lead to cost savings because plastic is the most expensive part. Practically all of these mostly inorganic components are only compatible with polymers after adding organosilanes. These organosilanes are able to chemically bond to the surface of filling and reinforcing substances. If these organosilanes do not possess non-functional alkyl groups, then the created hydrophobisation of surfaces is sufficient for significantly improving dispersibility. Higher process speeds, higher filling levels and in many cases even improved mechanical properties are achieved. Additional chemical bonding to the polymer is possible if silanes are functionalised with reactive organic groups. In these cases, silanes act as adhesive agents between the inorganic and organic matrix. Small quantities of silane are sufficient in order to achieve significant improvements because the bonds are chemically stable and function at a monomolecular level, a benefit already being commercially utilised in numerous applications. Meanwhile, used silane quantities significantly exceed 100,000 annual tonnes. Quantities on a scale of > 10 million tonnes/year result when calculated for compounds. The tyre industry is the leading industry in terms of quantities.
Glass fibre-reinforced plastics, in short GFP, are based on glass fibres that are treated with silanes.
Examples of filling and reinforcing substances include glass, titanium dioxide, kaolin, glimmer, aluminium and magnesium hydroxide, talcum, silicates, corundum, metal oxides or metal powder.
A whole range of physical properties can be improved with additives for the processing of polymer materials including mechanical resistance, scratch resistance, tensile strength, hardness, cohesion, ageing resistance and moisture resistance.
Additives also produce reduced water absorption of polymers and increased hydrophobia (= organophilia). Flame retardants such as Al(OH)3 or Mg(OH)2 achieve a sufficient flame delay.
Additives not only improve the end product. The manufacturing process is also optimised:
- Lower viscosity and/or higher throughput
- Simplified processing
- Reduced agglomerisation
- Higher filler content
- Lower total costs
So-called silane crosslinking is a large-scale technologically deployed variant for improving the mechanical properties of polymers. Vinylsilanes are grafted onto polymers, mostly polyethylenes or copolymerised with ethylene. The product can be crosslinked with moisture after formation. This is often used in order to improve the thermal stability of cable isolations or hot water pipes.
The usage of silanes is not just limited to thermoplastics. Artificial stones and synthetic resin concrete (epoxy, methacryl) or foundry resins (phenolic, furan resins, etc.) are typical applications for thermosetting plastics.
The addition of special silanes for catalytic propylene production creates a higher isotacticity, synonymous with increased crystallinity.
Polystyrenes
Polystyrenes are often used as substrates. One of the most noted application is peptide synthesis in which heterogenised amino acids and auxiliary reagents are used as so-called resins. The bonding to the polymer core is especially performed via the C-terminal end of the amino acids or via copolymerised trityl protection groups.
Crosslinked polystyrenes are produced with the copolymerisation of styrene with crosslinkers such as divinylbenzenes or other monomers with at least two terminal vinyl groups. The used quantities of these comonomers control the degree of crosslinking. Compared to non-crosslinked polystyrenes, crosslinked polymers possess significantly improved thermal stability. The tendency toward depolymerisation is also reduced.
Acrylates and polyacrylates
Many special allyl or vinyl-substituted monomers and crosslinkers are available in the abcr catalogue, among these acrylate or methacrylate ester.
Macromonomers such as PEG acrylates are used as linkers in biochemistry. Polyethylene glycol cores may exist as linear (monosubstituted and disubstituted PEG acrylates) or also in star form (three acrylate end groups or more per molecule).
Many special allyl or vinyl-substituted monomers and crosslinkers are available in the abcr catalogue, among these acrylate or methacrylate ester.
Macromonomers such as PEG acrylates are used as linkers in biochemistry. Polyethylene glycol cores may exist as linear (monosubstituted and disubstituted PEG acrylates) or also in star form (three acrylate end groups or more per molecule).
Polyacrylic acid is used in various areas of medicine, e.g. gel formers in the production of salves and gels for application to the skin and mucous membranes. Furthermore, polyacrylic acid also acts as a viscosity-increasing excipient in liquid medicinal products in order to prevent sedimentation and improve dosing. Polyacrylic acid acts as a bonding agent in tablets. Similar applications are well-known for poly(N-vinyl-2-pyrrolidones) or, in short, povidone.
Further monomer and polymer classes at abcr
Among the perfluorinated polymers, Teflon (= polytetrafluoroethylene) has become especially popular. It is used in chemical plant engineering based on its chemical resistance. Teflon has become well-known amongst the public especially due to its anti-adhesive effect as coating for frying pans. Teflon is also used in implants in medical engineering. Other perfluorinated monomers are also interesting as building blocks for fluoropolymers since the monomer tetrafluoroethylene is relatively elaborate in synthesis and processing.
Polyvinyl alcohol is produced with a controlled hydrolysis of polyvinyl acetate. Polyvinyl alcohol works as an emulsifier in mixtures and often has a high tensile strength and flexibility in pure form. These properties depend on humidity since the plastic absorbs water.
Diisocyanates and diols are converted in polyaddition in order to produce linear polyurethanes. Crosslinked polyurethanes can be produced by converting di and trifunctionalised isocyanates with diol/triol mixtures. Thermosetting plastics, thermoplastics or elastomers are created depending on the degree of crosslinking and the used isocyanate or alcohol monomers. The application area of polyurethanes extends to foams, lacquers, glues, coatings and floors.
Many polyimides are accessible by means of polycondensation of aromatic carboxylic acids and amines.
Polyimide fibres are extremely resistant to heat and mechanical wear. They are, e.g., used in protective clothing for forestry work since the spun fibres can hardly be penetrated by chainsaws and thus protect against serious injury.
New macromonomers can be created from PEG or polyolefin-based polymers as a basis for new copolymers by means of grafting or end group functionalisation.
Catalysts for polymerisation and oligomerisation
abcr offers a large variety of catalysts for the production of polyolefins such as polyethylene, polypropylene and copolymers from ethylene and higher alpha olefins.
These catalysts encompass the long-known Ziegler/Natta systems but also single-site catalysts such as metallocene complexes, bis(imino)iron complexes and salen-based phenoxy-imine zirconium complexes.
bis(imino)nickel complexes are used for the oligomerisation of ethylene and propylene. The resulting product has higher alpha olefins or branched olefins.